Rubber Injection Molding Machine - Direct Clamping
JD-RH series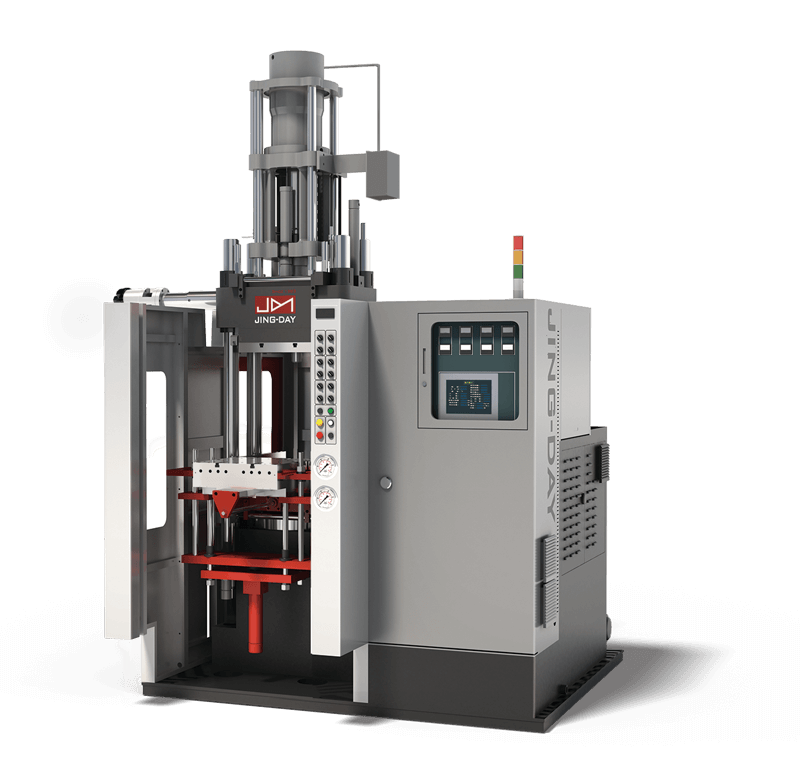
BACK
Features
- Machine for natural, synthetic, oil resistant,heat resistant and reclaimed rubber.
- High bed structure with direct clamping.
- PLC and HMI functional control as standard specification.
- Direct and indirect clamping structure.
- Specialized nozzle design to prevent material overflow.
- Specialized feeding device.
APPLICATIONS
Description
The JD-RH Series Direct Clamping Rubber Injection Molding Machine is a specialized piece of equipment used in the manufacturing of rubber products. This machine is designed to inject molten rubber into a mold under high pressure, creating a precise and accurate product. The Direct Clamping feature allows for the mold to be securely clamped in place during the injection process, resulting in a superior product with consistent quality.
Composition
- Human Machine Interface: Data is all displayed on the machine, including temperature control, pressure curve diagram, a flexible mechanism using function selection, freely setting production parameters and adjustment, self-programming mechanism action flow, production parameter setting memorize, and quick parameter setting selection.
- Injection system: The injection unit uses a hydraulic direct drive in 3 stages of pressure and 4 stages of flow. the material can be forced directly. This enables faster processing and stability for a variety of extended applications. The shot volume control by position transducer can have a very distinct output making it suitable with 0.7% tolerance accuracy.
- Charging unit: The automatic temperature control by heating oil. Stable temperature control for feeding area and material.
- Material alarm device: This device can check if there is any material (rubber stip) and the alarm will sound when the material is either cut off or has finished.
- Integrated hydraulic circuit: The hydraulic circuit system is designed with proportional and pressure valve control to provide excellent operating performance and highly precise products.
- Auxiliary double-cylinder: High-speed movement design, reduce cycle time, and increases production quantity.
- Temperature control device: The temperature control by PLC and SSR system. Ensure that screw feeding and charging area temperature is stable. preventing material vulcanization in the area.
- Safety screen: Use REER as the leader in Italy's optoelectronic safety sensor manufacturing. The infrared beam is used to detect the operator or object to ensure the safety of the operator and the machine. Depending on the operation of various types of machines, select. ing or performing different functions through the security interface, single or multiple beam detection can be used to satisfy most of the requirements or select various functions.
- Outside ejector: This device allows the mold to be separated, and can facilitate the function of removing or automatically ejecting the finished product, or flipping the mold as per user requirements.
- Core ejector: For multi-layer template design, the middle and upper sections of the mold can be fixed to this device.
- Lower platen sliding device: This device provides the convenience of the placement of raw materials and the removal of finished products. The device has been heating treated to increase service life.
Video
Specification
Model | JD-RH 65T | JD-RH 150T | JD-RH 200T | JD-RH 260T | JD-RH 300T | JD-RH 400T | JD-RH 500T | JD-RH 800T | |||||
---|---|---|---|---|---|---|---|---|---|---|---|---|---|
Shot Volum | c.c. | 300 / 500 | 500 /1000 | 1000 / 1500 | 1500 / 2000 / 2500 | 2000 / 2500 / 3000 | 2500 / 3000 / 4000 | 3000 / 4000 / 5000 | 7000 / 10000 / 12000 | ||||
Injection Pressure | kgf / cm² | 1600 | 1600 | 1600 | 1600 | 1600 | 1600 | 1600 | 1600 / 1100 /1100 | ||||
Injection Cylinder Pressure | kg / cm² | 150 | 150 / 140 | 140 / 150 | 150 | 150 / 150 / 140 | 150 / 140 / 170 | 140 / 170 / 150 | 150 | ||||
Injection Rate | c.c. / sec | 65 | 65 | 70 / 75 | 100 | 100 / 100 / 120 | 160 / 150 / 180 | 150 / 180 / 160 | 270 / 380 / 380 | ||||
Screw Diameter | mm | 32 | 45 | 45 | 45 | 50 | 50 | 50 | 65 | ||||
Strip Dimension (T x W) | mm | 6 x 30 | 10 x 60 | 10 x 60 | 10 x 60 | 10 x 60 | 10 x 60 | 10 x 60 | 10 x 60 | ||||
Clamping Force | ton | 65 | 150 | 200 | 260 | 300 | 400 | 500 | 800 | ||||
Plate Size | mm | 350 x 380 | 360 x 510 | 480 x 500 | 550 x 620 | 520 x 580 / 520 x 800 | 580 x 620 | 600 x 650 | 650 x 730 | 650 x 730 | 800 x 900 | 800 x 900 | 900 x 1000 |
Piston Diameter | mm | 200 | 310 | 355 | 400 | 430 | 500 | 560 | 700 | ||||
Piston Stroke | mm | 380 | 420 | 560 | 480 | 560 | 420 / 560 | 600 | 600 | 630 | 560 | 800 | |
Space Between Tie Bar | mm | 430 x 200 | 550 x 300 | 575 x 210 | 675 x 365 | 645 x 275 | 660 x 350 | 695 x 295 | 795 x 455 | 780 x 440 | 970 x 580 | 965 x 575 | 1100 x 630 |
Daylight Max | mm | 500 | 550 | 650 | 650 | 700 | 800 | 800 | 1200 | ||||
Oil Hydraulic System | HP | 7.5 | 10 | 15 | 20 | 25 | 30 / 30 / 40 | 30 / 40 / 40 | 50 | ||||
Hot Oil Cycling Motor | kw | 0.5 * 2 | 0.5 * 2 | 0.5 * 2 | 0.5 * 2 | 0.5 * 2 | 0.5 * 2 | 0.5 * 2 | 0.5 * 3 | ||||
Platen Heating Capacity | kw | 4.8 | 7.6 | 8 | 12.6 | 11.6 / 16.4 | 14.4 | 15 | 18.2 | 18.2 | 31 | 31 | Steam / Coal Oil |
System Pressure | kg / cm² | 210 | 210 | 210 | 210 | 210 | 210 | 210 | 210 | ||||
Oil Tank Capacity | liters | 280 | 350 | 430 | 430 | 470 | 560 | 560 | 700 | ||||
Machine Dimensions | mm | 1585 x 2610 x 2880 | 1585 x 2800 x 3520 | 1635 x 2960 x 3770 | 1635 x 3020x 3730 | 1635 x 3090 x 3940 | 1635 x 3080 x 3820 | 1745 x 3070 x 4530 | 1745x 3120 x 4550 | 1885 x 3200 x 4770 | 2085 x 3390 x 5000 | 2085 × 3390 × 4950 | 2385 x 3680 x 6520 |
Machine Weight (Approx) | kg | 3200 | 4800 | 5500 | 6200 | 6700 | 7300 | 8200 | 9000 | 9500 | 12800 | 14300 | 19200 |
*Dimensions are as standard, subject to change by options or upon custom-made;actual specifications are based on the finished products. *表內為標配尺寸,會因選配或客製化而有所差異,請以實際為準 |
Mold Installation & Heating Plate Dimension
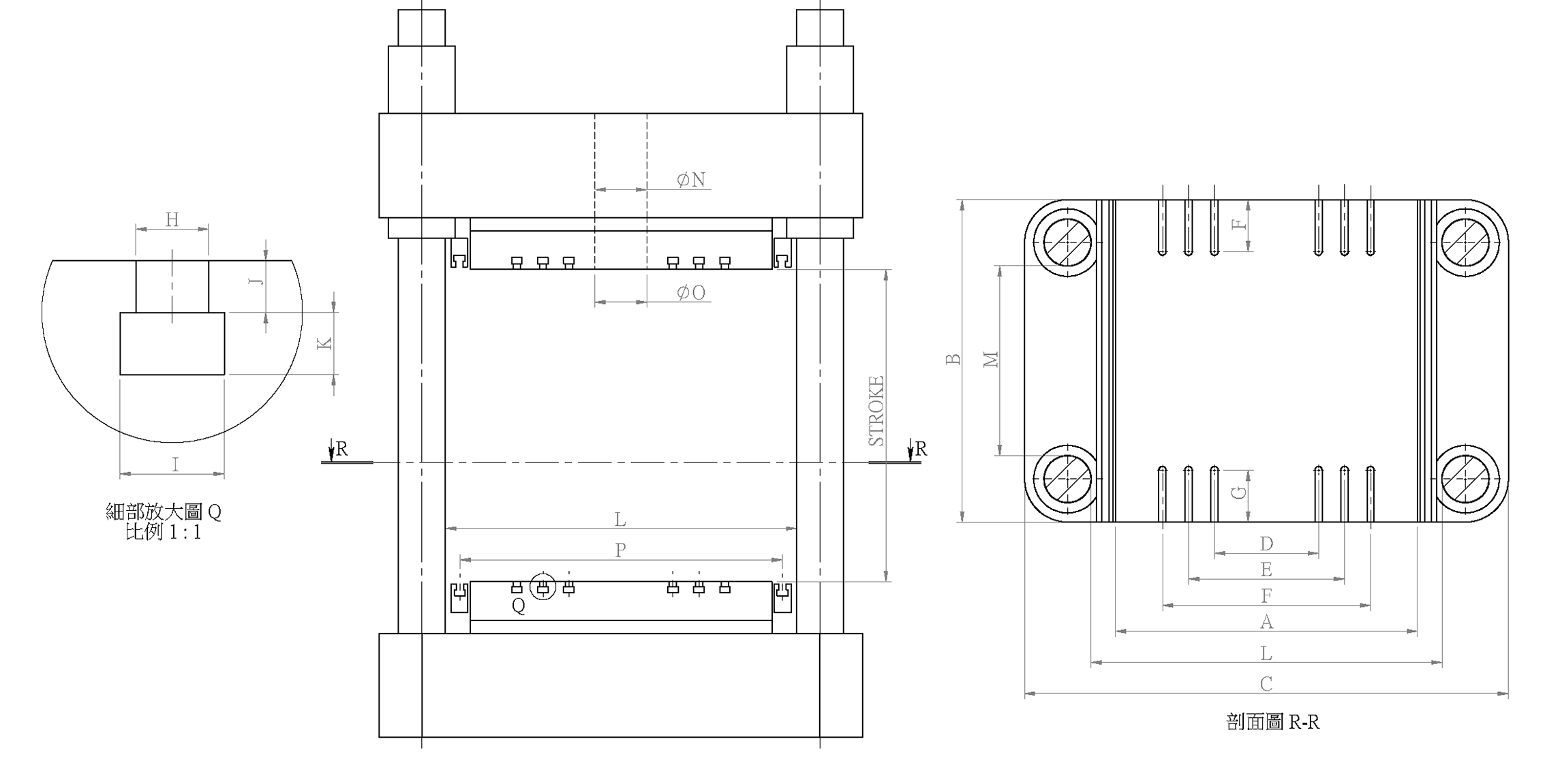
Model | JD-RH65T | JD-RH150T | JD-RH200T | JD-RH260T | JD-RH300T | JD-RH400T | JD-RH500T | JD-RH800T | |||||
---|---|---|---|---|---|---|---|---|---|---|---|---|---|
Stroke / Dimension | 380 | 420 | 560 | 480 | 560 | 420 / 560 | 600 | 600 | 600 | 630 | 560 | 800 | |
A (mm) | 350 | 450 | 480 | 550 | 520 | 580 | 600 | 650 | 650 | 800 | 800 | 900 | |
B (mm) | 380 | 510 | 500 | 620 | 580 | 620 | 650 | 730 | 730 | 900 | 900 | 1000 | |
C (mm) | 610 | 780 | 800 | 930 | 910 | 930 | 960 | 1060 | 1060 | 1290 | 1290 | 1470 | |
D (mm) | 150 | 150 | 200 | 200 | 200 | 200 | 200 | 200 | 200 | 300 | 300 | 300 | |
E (mm) | - | - | - | 300 | 300 | 400 | 400 | 400 | 400 | 500 | 500 | 500 | |
F (mm) | - | - | - | - | - | - | - | - | - | - | - | 700 | |
G (mm) | 90 | 120 | 120 | 120 | 135 | 145 | 145 | 145 | 145 | 200 | 200 | 250 | |
H (mm) | 14 | 18 | 18 | 18 | 18 | 18 | 18 | 18 | 18 | 18 | 18 | 28 | |
I (mm) | 20 | 25 | 25 | 25 | 25 | 25 | 25 | 25 | 25 | 25 | 25 | 39 | |
J (mm) | 10 | 10 | 10 | 10 | 10 | 10 | 10 | 10 | 10 | 10 | 10 | 20 | |
K (mm) | 12 | 12 | 12 | 12 | 12 | 12 | 12 | 12 | 12 | 12 | 12 | 17 | |
L (mm) | 430 | 550 | 575 | 675 | 645 | 660 | 695 | 795 | 780 | 970 | 965 | 1100 | |
M (mm) | 200 | 300 | 210 | 365 | 275 | 350 | 295 | 455 | 440 | 580 | 575 | 630 | |
N (mm) | 100 | 100 | 100 | 100 | 100 | 100 | 125 | 150 | 140 | 140 | 140 | 200 | |
O (mm) | 70 | 80 | 86 | 86 | 95 | 95 | 100 | 100 | 100 | 100 | 100 | 110 | |
P (mm) | 390 | 490 | 520 | 620 | 580 | 620 | 650 | 720 | 720 | 880 | 865 | 980 |
